Product Overview
S.P. Water Pumps Ltd are proud to be associated with the finest quality OEM Manufacturers in Europe.
S.P. Water Pumps Ltd are proud to be associated with the finest quality OEM manufacturers in Europe, enabling us to offer brand new high quality water pumps and oil pumps for diesel engines.
We offer the broadest range of brand new units for almost any engine within the marketplace at extremely competitive prices.
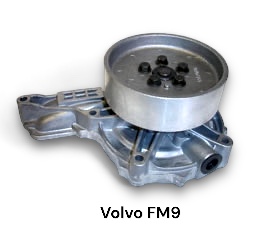
We are suppliers of the following:
Re-Manufacturing
We also supply re-manufactured water pumps for older or specialist engines that are longer available in the marketplace and for customers who prefer the lower cost of exchange units.
All of our exchange water pumps are re-manufactured to the very highest OEM specifications and with over 40 years experience in the market we have the professionalism and adaptability to meet the present and future demands of our customers.
All units are fitted with the very latest components, many of which are far superior to those originally fitted. A typical example is the mechanical seal, which due to advanced technology, is continuously being improved by the seal manufacturers and is becoming more sophisticated, better engineered and more capable than those of just 12 months ago!
Skilled Workforce
S.P. Water Pumps Ltd has a highly skilled workforce which has led to the company securing contracts to Re-Manufacture and Assemble Brand New Water Pumps with many Truck Manufacturers and Bus Companies.
Quality Assurance
We have implemented a quality assurance system working to ISO 9002 standards. Throughout re-manufacture written procedures are adhered to as laid down in our quality system which has been approved by our OEM customers.
- The pump is completely dismantled, and the bearings and seals discarded to be replaced with new.
- All parts, including the casing, are chemically cleaned, and then shot blasted. This allows us to thoroughly inspect for any damage and wear to determine serviceability.
- Only components which satisfy our high levels of quality are re-used whilst the remainder are discarded and replaced with new parts. New parts are sourced OE or if not available as is the case with many older engines we manufacture or repair in house.
- Final assembly is always completed by one member of staff who is responsible for the completed part. After final assembly the unit is pressure tested by another member of staff and will undergo a final quality check. Assembly and testing are separate operations and are always carried out by different members of staff. This results in the highest quality rating in the re-manufacturing field.
1000s
Models in stock
40
Informative in-house catalogues
44
Years of Experience
01925 85 00 82
Call us today!
Quality
We use only high quality parts in all of our water pumps.
All of our exchange water Pumps are re-manufactured to the very highest OEM specifications and are fitted with the very latest components, many of which are far superior to those originally fitted.
Some of the older water pumps we re-manufacture: vintage car, bus, truck etc. were originally fitted with what was available at the time of original manufacture.
We modify all of the older water pumps to the very latest specification seals and can guarantee a much improved and more reliable Water Pump.
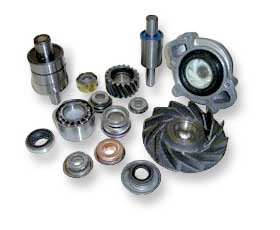
Water Pump Technical Information
All water pumps are very similar in design, the main differences being:
- The shape and size of the casting.
- The types of bearings used
- The type of seal used.
The water pump will be fitted into the engine block or will be externally mounted. The water pump will either be driven by a pulley fitted to the front of the unit, or will be gear driven from a gear drive fitted to the front of the unit. The source of power to drive the water pump will come mainly from the engine. The rear of the water pump will have an impeller fitted; this is what circulates or pumps the water around the engine.
The two most common causes for the failure of a water pump are:
Resulting initially in a noisy unit, but if run continuously in this state the bearings would disintegrate causing possible damage to the water pump and external damage to the engine.
The most common causes of bearing failure are:
- Natural wear.
- Too much tension on the fan belt.
- Excess radial loads caused by belt failure on multi belt pulleys.
- Out of balance fan assembly’s or pulleys.
- Lack of lubricant.
- Incorrect fitting of bearings during manufacture.
- Seal failure washing away bearing lubricant.
Resulting in the loss of water from the cooling system and overheating of the engine should temperature warning gauges be ignored.
The most common causes of seal failure are:
- Natural seal wear.
- Climatic changes.
- Running the engine without water in the cooling system.
- Bearing failure causing seal rock.
- Allowing the coolant to freeze and running the engine.
- Leaking head gasket or piston rings creating excessive pressure within the cooling system.
- Dirty coolant.
- Incorrect fitting of the seal during manufacture.
Types of Seals Used:
These seals are fitted into the water pump housing or impeller housing. The outer case of the seal can be made from either rubber or steel. These seals include a conical spring whose load is uniformly distributed round the periphery, and any pressure of the fluid to be sealed is added, to a certain extent to the spring action, thus ensuring very stable frictional contact. The use of the stationary seal requires the impeller to compress the seal to the correct working height.
The complete seal unit. These seals are by far the most superior seal available today. The seals are available in either rubber or steel. The advantage of using this type of seal is that the friction face is built into the seal, thus eliminating any possibility of foreign matter getting between the two seal faces during assembly. The inner sleeve of the seal is in permanent contact with the shaft, which reduces the possibility of fluid passing between the shaft and impeller. The rubber version of this seal requires the impeller to compress the seal to the correct working height. The steel version once inserted into the housing with the correct insert tool locks itself to the correct working height due to the interference fit between the shaft and inner sleeve of the seal. The only purpose of the impeller now is to pump fluid. The steel version in our opinion is the best available seal on the market.
These seals are designed for a push fit directly onto the shaft of the pump. These seals are used in conjunction with a counter-face which is usually inserted into the pump housing. The use of the rotary seal requires the impeller to compress the seal to the correct working height.
This is used in conjunction with a rotary or stationary seal; the inner bore of the counterface seals against the shaft and the friction face against the seal. The impeller is required to compress the counterface against the seal to the correct working height.
Types of Bearings Used:
Open deep groove ball bearing. This is the most widely used bearing.
These bearings are fitted with metal shield plates on either one or two sides.
These bearings are again similar to above but are fitted with metal reinforced synthetic rubber seals which are securely fixed in the outer ring and have a rubbing lip which contacts the inner ring in order to provide positive sealing at all times. The rubbing seals are effective at preventing the ingress of dirt and keeping grease in. These bearings are fitted with a seal on or two sides.
These bearings are suitable for heavy radial loads and high speed operation. The bearings are separable, which greatly simplifies mounting and dismounting even in the case of interference fits.
The construction of this bearing provides a high capacity for radial loads, axial loads in one direction and combined loads. These bearings are used in pair arrangements.
This is an integral shaft bearing and is accepted as the ideal bearing assembly for the use in automotive water pumps, because of their advantage in terms of cost, simplicity and performance.